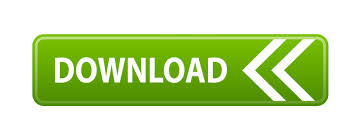
Rotary draw bending (RDB) is a precise technology, since it bends using tooling or "die sets" which have a constant center line radius (CLR), alternatively indicated as mean bending radius (Rm). Although a single die can produce various shapes, it only works for one size tube and radius. This process is used where a consistent cross section of the pipe is not required. Because the pipe is not supported internally there is some deformation of the shape of the pipe, resulting in an oval cross section. In this process a die in the shape of the bend is pressed against the pipe forcing the pipe to fit the shape of the bend. Press bending is probably the first bending process used on cold pipes and tubing. Pipe bending machines are typically human powered, pneumatic powered, hydraulic assisted, hydraulic driven, or electric servomotor. The pressure die and the wiping die are formed from aluminum or bronze to maintain the shape and surface of the work piece as it slides by. For example, the clamping block, rotating form block and pressure die are often formed from hardened steel because the tubing is not moving past these parts of the machine. However, when there is a concern of scratching or gouging the work piece, a softer material such as aluminum or bronze is utilized. Much of the tooling is made of hardened steel or tool steel to maintain and prolong the tool's life. A wiper die is usually made of a softer alloy such as aluminum or brass to avoid scratching or damaging the material being bent. The tube is held in tension by a wiper die to prevent any creasing during stress. For some tube bending processing, a mandrel is placed inside the tube to prevent collapsing. Other forms of processing including pushing stock through rollers that bend it into a simple curve. Often, stock tubing is held firmly in place while the end is rotated and rolled around the die. The process of tube bending involves using mechanical force to push stock material pipe or tubing against a die, forcing the pipe or tube to conform to the shape of the die. The tube is also loosely held by two other dies, the wiper die and the pressure die. Tube bending as a process starts with loading a tube into a tube or pipe bender and clamping it into place between two dies, the clamping block and the forming die. Depending on the bend angle, wall thickness, and bending process the inside of the wall may wrinkle. To reduce this the tube may be supported internally and or externally to preserve the cross section. One side effect of bending the workpiece is the wall thickness changes the wall along the inner radius of the tube becomes thicker and the outer wall becomes thinner. When calculating a two plane bend, one must know the bend angle and rotation (dihedral angle). A 2D tube has the openings on the same plane a 3D has openings on different planes.Ī two plane bend or compound bend is defined as a compound bend that has a bend in the plan view and a bend in the elevation. More complex geometries include multiple two-dimensional (2D) bends and three-dimensional (3D) bends. Common simple bends consist of forming elbows, which are bends, and U-bends, which are 180° bends. The very first machine went into service in 1996 and is still in production.Ī tube can be bent in multiple directions and angles. The first all-electric tube bending machine was invented in 1995 by UK company Unison Ltd.īased in Scarborough, North Yorkshire, Unison developed bending machines with 20mm, 40mm and 65mm tube capacity. Other factors involved in the bending process are the wall thickness, tooling and lubricants needed by the pipe and tube bender to best shape the material, and the different ways the tube may be used (tube, pipe wires). However, square and rectangular tubes and pipes may also be bent to meet job specifications. Generally, round stock is used in tube bending. Freeform-bending processes, like three-roll-pushbending, shape the workpiece kinematically, thus the bending contour is not dependent on the tool geometry. These processes can be used to form complex shapes out of different types of ductile metal tubing. Straight tube stock can be formed using a bending machine to create a variety of single or multiple bends and to shape the piece into the desired form. Tube bending may be form-bound or use freeform-bending procedures, and it may use heat supported or cold forming procedures.įorm bound bending procedures like “press bending” or “rotary draw bending” are used to form the work piece into the shape of a die. Tube bending is any metal forming processes used to permanently form pipes or tubing.
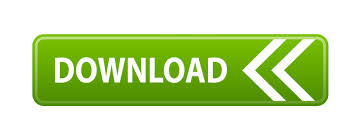